Honeycomb paper machines: Learn about honeycomb paper machines and their role in eco-friendly packaging.
Honeycomb paper machines are integral to producing eco-friendly packaging solutions that are increasingly replacing traditional plastic materials. These machines produce honeycomb paper used for cushioning and protective packaging, which is biodegradable and recyclable. In this article, we will explore various honeycomb paper machines available on the market, focusing on their technical features, quality, functions, and applications. A comparative analysis of these machines will also be provided using detailed tables.
1. Types of Honeycomb Paper Machines
Honeycomb paper machines vary based on their functionalities, ranging from manual cushion machines to fully automatic paper core machines. Below are some key types:
- Automatic Honeycomb Paper Machine: Designed for high-speed production of honeycomb paper cushioning with advanced automation features.
- Hydraulic Honeycomb Punching Machine: Specialized in punching honeycomb structures, offering adjustable thickness and pressure settings.
- Honeycomb Paper Core Machine: Produces continuous honeycomb cores with high efficiency and minimal labor requirements.
- Manual Honeycomb Paper Cushion Machine: A simple, portable machine suitable for small-scale or on-demand packaging needs.
- Honeycomb Paper Express Bag Making Machine: Focuses on producing honeycomb paper express bags as an eco-friendly alternative to plastic bubble wrap envelopes.
2. Applications of Honeycomb Paper Machines
Honeycomb paper machines are utilized across various industries due to their versatile applications. The finished products are used for:
- Packaging: Cushioning for fragile goods such as ceramics, glassware, electronics, cosmetics, and medicines.
- Logistics: Protective wrapping for transportation, minimizing product damage.
- Express Delivery: Honeycomb paper bags for e-commerce and logistics services.
- Retail: Eco-friendly packaging for retail items, ensuring a unique unboxing experience.
3. Comparative Analysis of Honeycomb Paper Machines
The following tables provide a detailed comparison of different honeycomb paper machines in terms of technical features, quality, functions, and applications.
Table 1: Technical Features of Honeycomb Paper Machines
Feature | Automatic Honeycomb Paper Machine | Hydraulic Punching Machine (HHBP-1612) | Honeycomb Paper Core Machine (CX-1600) | Manual Cushion Machine (HC10) |
---|---|---|---|---|
Voltage | 380V 3 Phase | 220V/380V/415V | 380V | Manual (No power needed) |
Max Width | 508mm | 1600mm | 1600mm | NA |
Speed | 0-200m/min | 180mm/min | 380 cuts/min | Manual operation |
Power | 3 KW | 3.0 KW | 60 KW | NA |
Dimensions (L x W x H) | 3500 x 1640 x 1800mm | 2300 x 1600 x 1600mm | 32m total length | Portable |
Weight | 1800 KG | 3500 KG | NA | Lightweight |
Control System | PLC Automated | Hydraulic + Electric System | PLC Control | Manual operation |
Unwinding/Rewinding Diameter | 1200mm/300mm | Not applicable | Not applicable | Not applicable |
Table 2: Quality and Features
Quality & Features | Automatic Honeycomb Paper Machine | Hydraulic Punching Machine (HHBP-1612) | Honeycomb Paper Core Machine (CX-1600) | Manual Cushion Machine (HC10) |
---|---|---|---|---|
Material Compatibility | Kraft Paper, Fish Net Paper | Kraft Paper | Kraft Paper | Honeycomb Paper Rolls |
Max. Punching Thickness | Not applicable | 60mm | NA | NA |
Hydraulic Pressure | NA | 50T | NA | NA |
Automation Level | Full | Semi-Automatic | Fully Automatic | Manual |
Special Features | Inverter for speed regulation, automatic meter counting, ultrasonic web guide | Low noise oil pump, thermal refining | High-speed cutting, electric heating | Portable, easy to use, no power needed |
Table 3: Functions and Applications
Functions & Applications | Automatic Honeycomb Paper Machine | Hydraulic Punching Machine (HHBP-1612) | Honeycomb Paper Core Machine (CX-1600) | Manual Cushion Machine (HC10) |
---|---|---|---|---|
Primary Function | Die-cutting and wrapping | Punching honeycomb structures | Producing honeycomb cores | Cushioning paper dispenser |
Application Areas | Logistics, Retail, Fragile Goods | Industrial Packaging | Packaging Material Production | Small businesses, e-commerce |
Eco-Friendly Features | Yes (degradable packaging) | Yes (minimal waste) | Yes (efficient resource use) | Yes (manual operation, no electricity) |
Operational Flexibility | High (adjustable speed) | Medium (manual adjustment needed) | High (automatic control) | Low (manual adjustment only) |
4. Technical Process of Honeycomb Paper Machines
4.1. Automatic Honeycomb Paper Machine
This machine automates the entire process from unwinding to cutting and rewinding. The operation begins with feeding kraft paper into the system. The machine features an ultrasonic web guide for precise control, and the magnetic powder brake regulates tension. The pneumatic cylinder controls the cutting module, and the finished rolls are automatically changed. This setup ensures efficient production with minimal manual intervention.
4.2. Hydraulic Honeycomb Punching Machine
The HHBP-1612 model is designed for punching honeycomb structures with high precision. It utilizes a hydraulic system with a double-cylinder setup for consistent pressure. The process involves placing the material on the working area, where the hydraulic cylinders press the paper to create honeycomb holes. The hydraulic system ensures accurate and powerful punches, while the electric system manages speed and control.
4.3. Honeycomb Paper Core Machine (CX-1600)
This machine produces continuous honeycomb cores by processing base paper rolls through various stages, including gluing, drying, pressing, and cutting. The fully automated PLC control system minimizes human error and maximizes output efficiency. It handles multiple paper rolls simultaneously, ensuring a steady production line with minimal downtime.
4.4. Manual Honeycomb Paper Cushion Machine (HC10)
The HC10 is a straightforward machine that requires manual operation. The honeycomb paper is manually stretched to create cushioning material. This is particularly suitable for small businesses or e-commerce stores needing flexible, on-demand packaging solutions.
5. Market Trends and Environmental Impact
The global market trend is shifting towards sustainable packaging solutions. Several countries, including the EU, USA, Japan, and Australia, have implemented legislation banning foam and plastic packaging materials, encouraging the use of biodegradable alternatives like honeycomb paper. The demand for honeycomb paper machines is therefore increasing as companies seek to meet these regulatory requirements and enhance their green credentials.
The biodegradable and recyclable nature of honeycomb paper makes it a viable solution for companies looking to reduce their environmental footprint. Machines like the Honeycomb Paper Express Bag Making Machine are designed to replace traditional plastic bubble wrap envelopes, providing a 100% recyclable alternative.
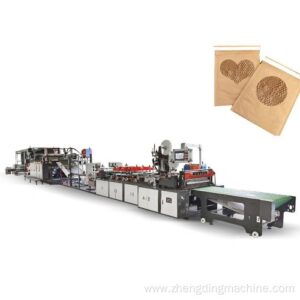
6. Conclusion
Honeycomb paper machines offer diverse functionalities and are crucial in the evolution of sustainable packaging solutions. From fully automated production lines to manual, portable machines, these solutions cater to various industries and business sizes. Investing in honeycomb paper machines aligns with global sustainability trends and offers businesses a competitive edge by providing eco-friendly packaging alternatives.
As the demand for sustainable solutions rises, manufacturers like AMC Machinery, Zhengding, and other OEM providers continue to innovate, producing advanced models with better efficiency, quality, and environmental compatibility. Businesses aiming to meet environmental standards and optimize packaging processes should consider these machines as valuable assets for long-term growth. We recommend the best suppliers to customers who are in need of the best machine. Don’t hesitate to contact us for referrals.