Comprehensive Guide to Honeycomb Paper Making Machines: Features, Functions, and Competitor Comparison
Introduction
The honeycomb paper making machine is a vital tool in the packaging industry, producing lightweight and eco-friendly honeycomb paper products. These machines are designed to create honeycomb paper structures used in packaging items like glass, ceramics, and gifts, providing a sustainable alternative to plastic foams. This article explores different types of honeycomb paper making machines from various manufacturers, examining their technical features, quality, functions, usage, processes, and applications. It also provides a comparative analysis of several models available in the market.
1. Overview of Honeycomb Paper Making Machines
Honeycomb paper making machines are highly efficient systems that streamline the production of honeycomb paper, ensuring speed, consistency, and quality. Typically, these machines are divided into two main sections: the honeycomb paper core line and the honeycomb paperboard lamination line. The core line produces the honeycomb structure, while the lamination line applies surface paper to the honeycomb core, creating sturdy honeycomb paperboard.
2. Types of Honeycomb Paper Making Machines
There are various types of honeycomb paper making machines based on automation level, production speed, and customization capabilities:
-
- Fully Automatic Honeycomb Paper Making Machine: A high-efficiency system capable of 24-hour production with minimal manual intervention. It uses integrated circuit controls and offers stable operation with automatic correction systems.
- High-Speed Honeycomb Core Machine: Designed for high productivity, these machines feature multiple paper stands, gluing stations, and cutting units, ensuring efficient production of honeycomb cores.
- Semi-Automatic Honeycomb Paper Machines: These are suitable for smaller operations where partial manual intervention is acceptable, offering flexibility in customization.
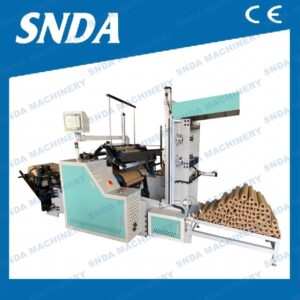
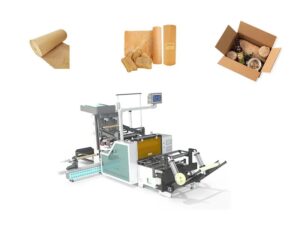
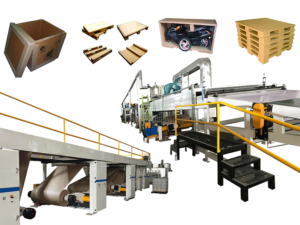
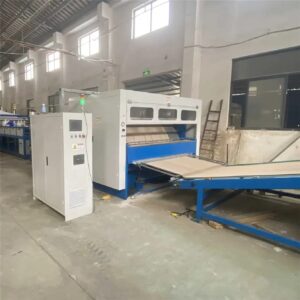
3. Technical Features of Honeycomb Paper Making Machines
Below is a comparison of technical features from different manufacturers:
Feature | OEM Honeycomb Paper Machine | Fully Automatic (Found) | High-Speed Honeycomb Core Machine |
---|---|---|---|
Max Working Area | 1600×1200 mm | 1800 mm | 1600-2000 mm |
Stroke | 60-260 mm | N/A | N/A |
Punching Thickness | Up to 60 mm | N/A | N/A |
Power | 3.0 kW | 60 kW | 60 kW |
Hydraulic Pressure | 50T | Variable | N/A |
Cutting Speed | 180 mm/min | High-speed | High-speed, heavy-duty |
Weight | 3500 kg | N/A | N/A |
Customization Options | Available | In-depth (logo, color) | Mechanical or hydraulic paper stand options |
This table highlights that different machines cater to various production needs, from small-scale, precise operations to large-scale, high-speed productions.
4. Functions and Features of Honeycomb Paper Making Machines
Each honeycomb paper making machine offers distinct features and functions aimed at improving efficiency and quality:
-
- OEM Honeycomb Paper Machine:
- Uses Q235 steel for durability.
- Equipped with a low-noise oil pump and treated oil cylinders for high-temperature resistance.
- Offers separate hydraulic and electric systems for safety and efficiency.
- Fully Automatic Honeycomb Paper Machine:
- Provides continuous, 24-hour production.
- Intelligent automated functions ensure stability and minimal wastage.
- Features such as variable frequency speed regulation and automatic correction enhance reliability.
- High-Speed Honeycomb Core Machine:
- High productivity with multiple gluing stations and heating units.
- Adjustable cell sizes (4-25mm) for various product requirements.
- Supports high-speed, heavy-duty cutting and has options for breath holes and other customizations.
- OEM Honeycomb Paper Machine:
5. Usage and Process of Honeycomb Paper Making Machines
Usage: Honeycomb paper making machines are used to produce honeycomb paper and paperboards, which serve as eco-friendly packaging materials. These products are lightweight yet durable, making them suitable for packing fragile items like ceramics, glass, electronics, and gift items.
Process: The production process of honeycomb paper involves the following steps:
-
- Paper Unrolling: The paper is unwound from jumbo rolls and prepared for processing.
- Gluing and Laminating: The paper core is coated with adhesive and laminated to form the honeycomb structure.
- Die-Cutting and Folding: The machine cuts and folds the paper into the required shapes and sizes.
- Drying and Pressing: The laminated paper is dried and pressed to ensure strength and stability.
- Cutting and Stacking: The final product is cut to size, stacked, and prepared for packaging.
6. Applications of Honeycomb Paper Making Machines
Honeycomb paper has a broad range of applications, including:
-
- Packaging: Protecting fragile and valuable items during transportation.
- Furniture Manufacturing: Used as a core material in lightweight furniture for increased durability without added weight.
- Automotive Industry: Utilized in vehicle interior components for their lightweight and impact-resistant properties.
- Construction: Applied in temporary walls or panels as an eco-friendly building solution.
7. Quality and Efficiency Analysis
Different manufacturers offer varying levels of quality, efficiency, and reliability in their honeycomb paper making machines. Here’s a comparison based on these criteria:
Manufacturer | Quality | Efficiency | Reliability | Customization |
---|---|---|---|---|
OEM (China) | High, using premium steel materials | Moderate, suitable for SME | Reliable with thermal refining treatment | Available, focused on standard options |
LabeMachine Automation | Standard industrial quality | High-speed, cost-efficient | Stable with low maintenance | Basic logo and color customization |
Found (Xiamen) | Premium, automated correction system | Very high, fully automated | Highly reliable with continuous operation | In-depth customization available |
This analysis shows that machines like the one offered by “Found” provide higher efficiency and greater reliability, ideal for companies looking for robust and continuous production capabilities. In contrast, OEM machines are suitable for medium-scale operations where durability and efficiency at a moderate pace are required.
8. Competitor Comparison
Here’s a detailed comparison of honeycomb paper making machines from three prominent competitors:
Parameter | OEM (China) | LabeMachine Automation | Found (Xiamen) |
---|---|---|---|
Automation Level | Semi-automatic | Semi-automatic to automatic | Fully automatic |
Production Capacity | Moderate | High | Very high |
Power Consumption | 3.0 kW | 45 kW | 60 kW |
Customization Capability | Limited | Basic | Extensive |
Price Range | Budget-friendly | Mid-range | Premium |
From this table, it is evident that the choice of machine depends on the scale and needs of the business. Smaller businesses may opt for OEM machines for cost efficiency, while larger firms seeking automation may prefer “Found.”
9. Conclusion
Honeycomb paper making machines are crucial for producing sustainable and efficient packaging materials. The variety of machines available caters to different production scales and needs, from semi-automatic models for smaller businesses to fully automated, high-speed systems for larger industries. The choice of machine ultimately depends on factors like production capacity, automation level, and customization needs.
This comparative analysis provides insights into the technical features, quality, and efficiency of honeycomb paper making machines, helping businesses select the best fit for their operations while advancing the eco-friendly packaging industry. Additionally, we recommend customers to the best suppliers. If you are in need of any honeycomb paper making machine for your specific needs, don’t hesitate to contact us for referrals.